Cosmo’s Air Leak Testers
AIR LEAK TESTER
Cosmo’s Air Leak Testers support the creation of high-quality products
There are many airtight products that are familiar to us.
Leak testers are essential in the production of these products to ensure the safe use of quality products.
Cosmo’s Air Leak Testers are widely used in many industries and boast the top market share in Japan and the world.
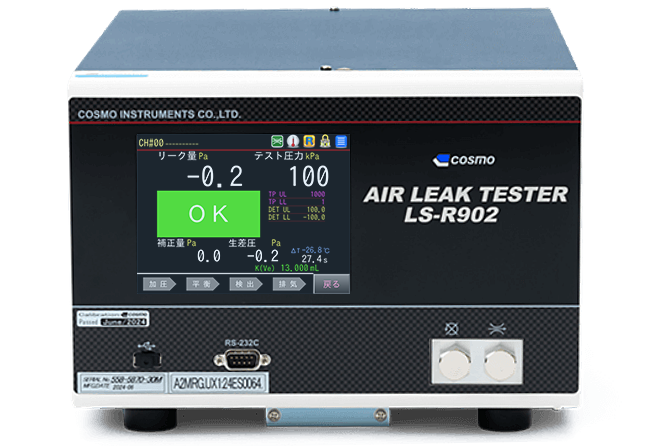
Features 01
Cumulative production
and shipment of over
100,000 units
Applications of Air Leak Testers have expanded to include medical equipment, housing equipment, electronic components & electrical equipment, and food containers.
Products for different applications require different performance specifications.
We have been researching and developing the best test method for each of the specifications, such as leak testing of containers several liters in size and leak testing of sealed electronic components as small as a few cubic millimeters.
More than 100,000 units of Air Leak Testers have been shipped to the market and are used in various industries.
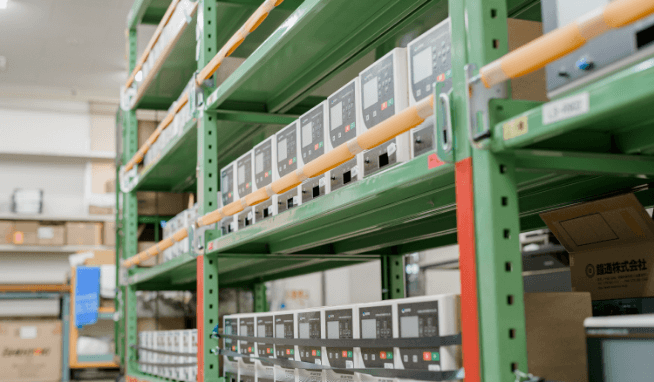
Features 02
Sold in 13 countries
In the 1989s, we established representative offices in the U.S. and Korea and an overseas office in Taiwan to provide support to our overseas customers.
Today, we have offices in 13 countries, including China, Southeast Asian countries, and India. In many of these countries, we are already able to provide the same quality of service as in Japan through our dedicated leak testing staff.
We will continue to make every effort to ensure that our leak testers can be used with confidence in all countries.
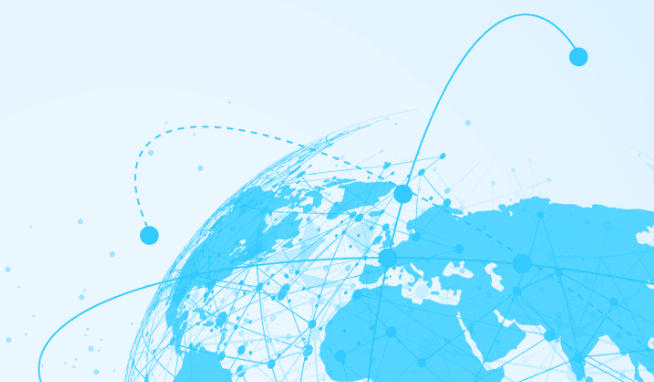
Features 03
High durability achieved over 10 million times
A differential pressure sensor with high sensitivity of 0.1 Pa and high differential pressure resistance of 5 MPa is installed as standard, and high measurement repeatability and leak sensitivity can be obtained through the Intelligent Pneumatic Circuit with originally developed air-operated valves.
The differential pressure sensors we developed can be used with the same sensitivity characteristics even when the maximum operating pressure is applied more than 10 million times.
We have now solved various problems and are offering leak testers that can withstand test pressures up to 16 MPa.
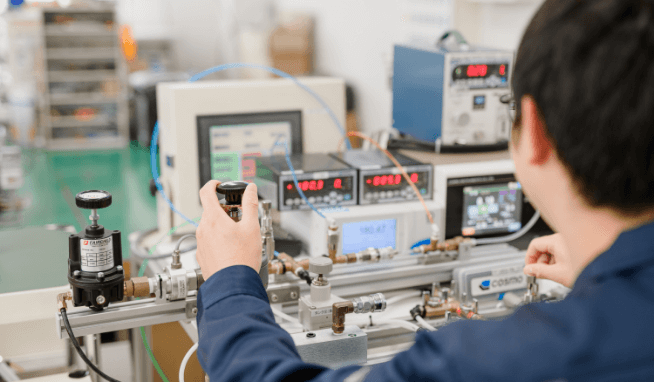
Features 04
14 locations nationwide Prompt service
It is also important to have a service system that can respond quickly and appropriately in the event of a breakdown or failure.
We have eight sales offices and six service centers throughout Japan.
We have a complete system in place with specialized staff for everything from before- and after-sales service, which is indispensable for leak testers.
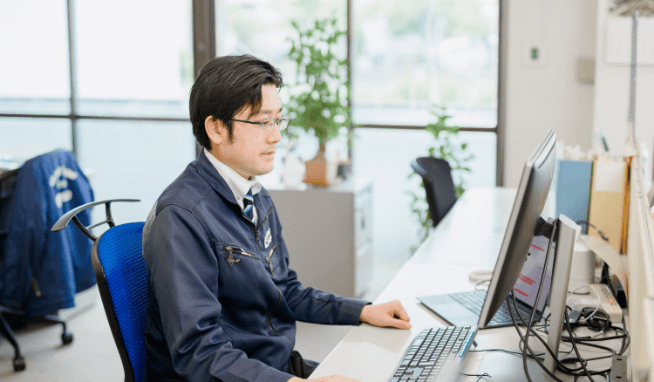
What are required of Air Leak Testers
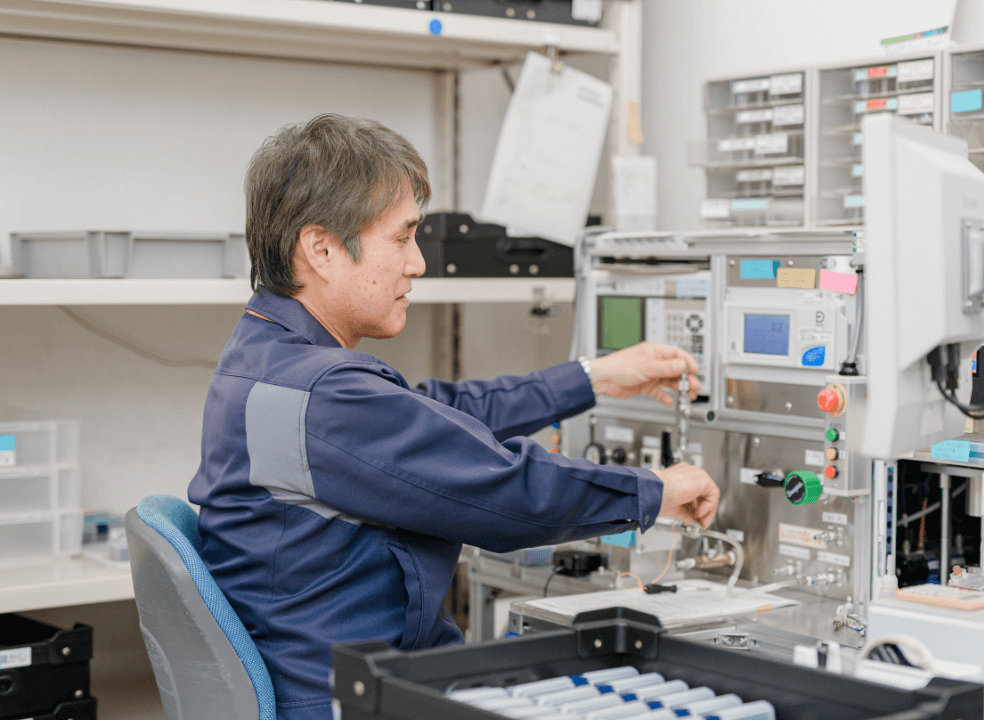
We take responsibility for leak testing
Leak testing is not only for accurately detecting slight pressure changes caused by leaks. It is necessary to find different causes of pressure changes other than leaks to suppress the effects of them.
Many of the causes are in the test environment, such as the work clamping and sealing devices, fixture piping, and ambient temperature. Sometimes the work itself has problems such as deformation, temperature changes, and internal leaks.
The technology to comprehensively analyze and address these issues is the air leak testing technology that is required of us as a manufacturer. Our role is to provide this technology, and we promise our customers that we will be responsible for leak testing until the very end.
We meet the high reliability required
We believe that strongest requirement for leak testers is reliability, and that our responsibility for leak testing leads to customer confidence.
For this purpose, Cosmo Instruments provides products that give reassurance to customers in any operating environment, and provides technical support to ensure that customers can use them properly.
Proven superior durability and few failures
High durability and failure-free operation are important for testers used on production lines.
Troubles due to line stoppage or misjudgment caused by breakdown can cause serious damage, and if breakdowns are frequent, spare testers will also be needed.
Our leak testers are the most widely used in Japan, and have been proven to have excellent durability and few failures, earning them praise from many customers.
Problem associated with the method of judging zero differential pressure as Pass
Almost all manufacturers of differential pressure leak testers share a common problem.
The problem lies in the method of leak testing that the testers make a Pass judgment on the works if the differential pressure is below a certain value and close to zero.
In other words, there is a problem that if the output of differential pressure sensor stops, if the valve does not work, or if there is a short circuit or leak inside the valve or differential pressure sensor, then no differential pressure is detected even if there is a leak.
Until the sensitivity is checked using a leak master, the defect will not be detected and leaking products will be judged as Pass.
If this defect is overlooked, it could develop into a serious recall. However, the reality is that many leak tester manufacturers have not taken sufficient measures to address this issue.
We have taken the following measures to avoid the risks.
- Measure 01
-
Thorough check on the sensitivity of differential pressure sensor
At the end of each test, air is blown and the differential pressure that occurs at this time is measured with the differential pressure sensor so that its output can be checked.
- Measure 02
-
Periodic automatic sensitivity check
Equipped with Automatic Leak Calibrator or Leak Master, it is possible to run an automatic sensitivity check periodically.
- Measure 03
-
Poppet valves resistant to dust and other foreign matter
We use poppet air valves that are resistant to dust and other foreign matter.
The poppet valves can be used safely for a long time without maintenance because the automatic grease supply from the lubricating wiper built into the bearing provides a high durability of 10 million times, and the valve operation failure due to oil loss or dust and the degradation of sensitivity due to internal leak can be structurally kept to a minimum. - Measure 04
-
Monitoring Test Pressure
At each stage in a leak test cycle, the test pressure is monitored to check the supplied pressure and the operation of each valve.
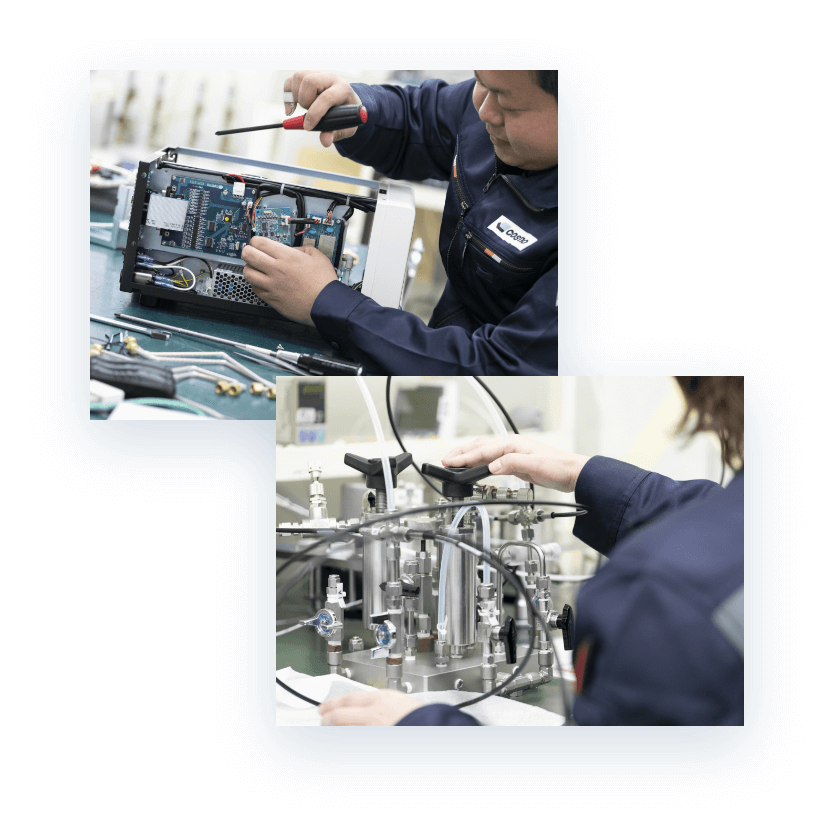
We will continue creating value by measuring “leaks”
We have faced many problems, solved them, and built up a track record of success.
We have developed a sealing material which is extremely low in hardness and is superior in strech and durability.
It can be used in sealing uneven surfaces and cast surfaces, enabling leak testing of works with shapes which were conventionally difficult to test.
This was realized in response to customer requests, and has prompted further development of our leak testing technology.
However, there are still inadequacies. A major issue with leak test is the effects of work and environmental temperatures. We are working on developing the methods suited to each case, including the development of a temperature compensation unit that compensates for temperature effects based on the correlation characteristics with the surface temperature of the works.
We have been and will continue to make every effort to further improve the performance of our products for reliable “leak” measurement and to solve our customers’ problems.