Various test methods and their selection
Consider and combine the various methods below to select the best one for your work.
Select by test pressure
Scroll
Advantages | Disadvantages | ||
---|---|---|---|
Pressurization method |
|
|
|
Vacuum method |
|
|
|
Select by work shape
Scroll
Advantages | Disadvantages | ||
---|---|---|---|
Differential pressure method |
|
|
|
![]() Normal method. To improve detection accuracy and reduce test time, insert cores so that the work volume is as small as possible. |
|||
Pressure change chamber method |
|
|
|
![]() For works with a large internal volume or those that are easily sealed in a capsule, measuring the leaking side at atmospheric pressure reduces test time |
|||
Sealed chamber pressure change method |
|
|
|
![]() This method is used for sealed works. |
Other applications of test method
Simultaneous testing of multiple works
- Method: Tests multiple works simultaneously.
- Target: Used for works with small internal volume or when there is sufficient margin for detection. Used when a longer Pressurization time is required (e.g., when there are deformation effects).
- Advantage: Shorter test time per work.
- Disdvantage: Cannot be used when accuracy is required or when the defect rate is high. Multiple test fixtures are required.
Simultaneous measurement of two chambers
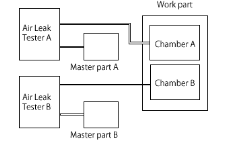
- Method: When a work has two chambers for separate measurement, use two testers to apply a different test pressures to each chamber and measure simultaneously.
- Advantage: Test time is reduced.
- Disadvantage: If leak occurs between the chambers A and B, the tester with high test pressure will judge the work as Fail, while the tester with low test pressure will judge the master as Fail, so caution is needed when processing the judgment signals.
- Exhaust Interference Prevention: If one tester completes judgment and exhausts first, it may affect the measurement of the other tester. To cope with it, tester models that can be externally controlled to have simultaneous exhaust are also available.