Advantages of Air Leak Testers
Leak testing in mass production lines for automotive and gas equipment components has traditionally been one of the bottleneck processes.
The method of visually checking for air bubbles by submerging the work in water after sealing is commonly used, but it has drawbacks such as possible oversights, the need for a drying process, and difficulty of automation.
Many alternative testers have been used, but they have shortcomings in terms of sensitivity, pressure resistance, running cost, handling, etc.
The differential pressure Air Leak Testers have been improved in place of the conventional methods and used as the most effective automatic leak testers.
Advantages of using Air Leak Testers
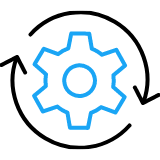
- Automates processing
- Saves manpower
- Easy operation, No skill required
- Improves work environment
- Easy maintenance
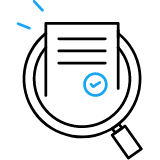
- Improves test performance
- Quantifies leak specifications
- Reduces defect rates
- Statistically processes and analyzes data
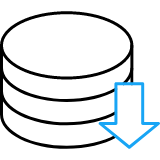
- Lowers complaints
- Improves yield
- Requires no drying process
- Reduces test time
- Lowers running costs
Comparison of water-dunk test, bubble test and Air Leak Tester
Air Leak Tester | Water-dunk test, Bubble test | |
---|---|---|
Automation | Automation |
Burdens workers |
Numerical management | Data management possible, Improves test performanceP |
Individual differences in detection |
Drying process | Not required |
Required |
Introduction of Air Leak Tester and leak specifications
To introduce Air Leak Tester, it is requiredl to set a quantified leak specification. It is necessary to determine what range of leak is acceptable by comparing with the conventional water-dunk test or by verifying under actual conditions.
It can also be determined with reference to past cases or specifications for similar works. The leak detection capability of leak testers depends on test conditions such as test time and test pressure. By using several non-leaking works and a reference leak (Leak Master) and performing some tests under different conditions, the actual performance of detection can be known from the data.
Leak units
- atm·mL/s or atm·mL/min
The volume of air leaking into the atmosphere per second or per minute. “atm·” is often omitted.
L μgr/s or μgr/min
The weight of air leaking into the atmosphere per second or per minute.
1 µgr (microgram) => 0.83 × 10-3 mL (1 atm, 20℃) - Lusec
Leak with a pressure increase of 1 μHg per second in a 1 L vacuum vessel.
1 Lusec=1/760 mL/sec≒1.32×10-3 mL/s - Torr・L/sec
Leak with a pressure increase of 1 Torr per second in a 1 L vacuum vessel.
1 Torr・L/s=1000 Lusec≒1.32 mL/s - Pa・m3/s
1 Pa・m3 /s = 9.869 atm・mL/s
1atm・mL/s = 1.013 × 10-1 Pa・m3/s
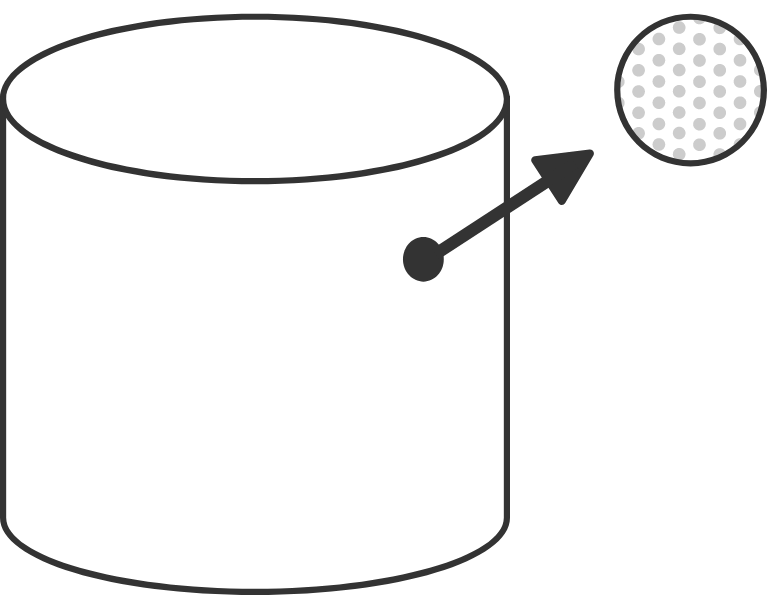
※ Leak represents the volume at atmospheric pressure
Types of leak detection methods
Water-dunk test, Bubble test
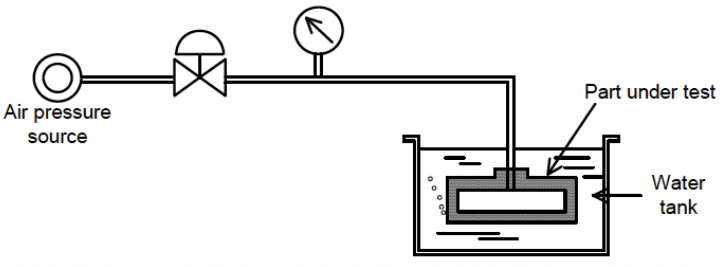
Pressurized air is sealed inside the work, and the work is then immersed in water or coated with soapy water to visually check air bubbles.
Tracer gas leak test
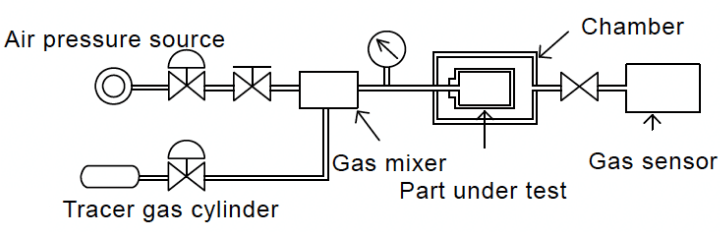
A gas (hydrogen, helium gas, organic halogen gas or chlorofluorocarbon gas) not present in the air is mixed with compressed air and sealed inside the work as a tracer gas to detect the gas leaking into the sealed container (chamber) containing the work with a gas detector (hydrogen leak detector, helium leak detector, etc. ).
(Applicable: Helium/hydrogen/battery leak test)
Flow measurement
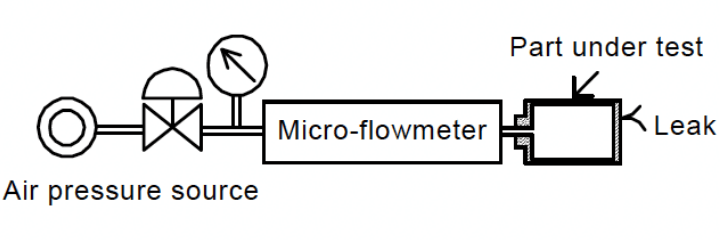
Since the leak rate is equal to the flow rate, the leak can be measured by feeding air into the work through a micro flow meter.
(Applicable: Air Flow Tester AF-R221)
Pressure decay method, Vacuum decay method
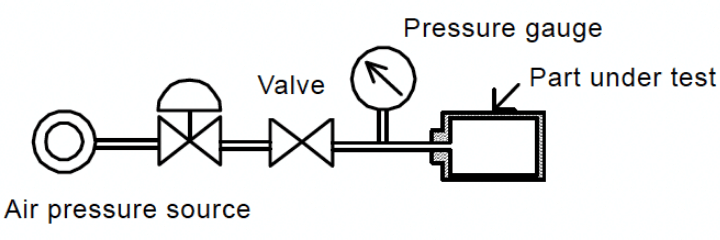
Positive or vacuum pressure is applied. The pressure drop over time due to leak after sealing with a valve is then detected by a pressure gauge, pressure sensor, or pressure switch.
(Applicable: Digital Pressure Gauge DP-340BA)
Differential pressure method
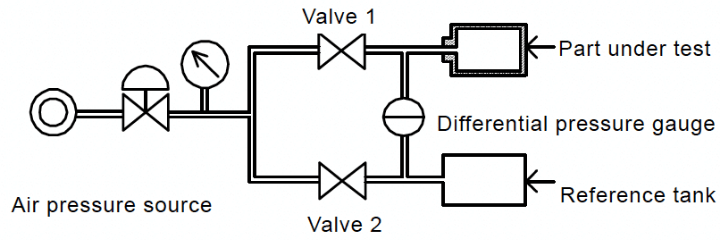
This method uses a differential pressure gauge (U-tube, differential pressure sensor, etc.) instead of a pressure gauge to detect the pressure drop due to leak as a differential pressure with the master tank with high sensitivity.
(Applicable: Air Leak Tester)
Distortion detection method
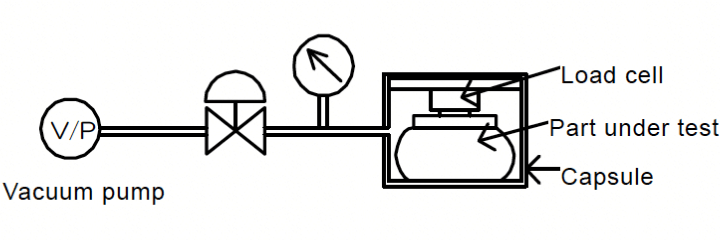
This method is used for packaged goods such as confectionery and medicines (e.g., pillow packaging).
When a package containing air is placed in a capsule and the inside of the capsule is evacuated, the package expands, but if the package has a leak, it does not expand.
The expansion is detected as distortion.
Water-dunk test, Bubble test
- Very good
- Good
- Not so good
- Bad
Leak detection method | Automation | Detection capability | Reliability | Durability | Versatility | Economy |
---|---|---|---|---|---|---|
Water-dunk test, Bubble test | ||||||
Tracer gas leak test | ||||||
Flow measurement method | ||||||
Pressure decay method, Vacuum decay method |
||||||
Differential pressure method | ||||||
Distortion detection method |